Pb-Free Electronics Risk Management (PERM) Council
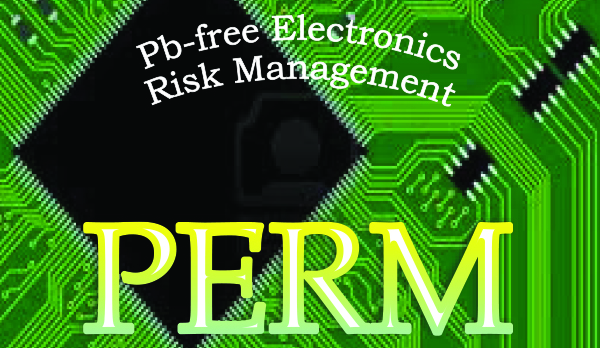
There is no electronics market sector currently immune from Pb-free. Ask yourself the following questions:
- Is your company already dealing with Pb-free electronics?
- Are Pb-free electronics required by your customers?
- Do you build products for any of the following harsh environments?
- Aerospace
- Medical
- Military
- Automotive
- Do your products require a long service life?
If you answered YES to any of these questions, there is a FREE and open global industry consortium available to help you and your company – the Pb-Free Electronics Risk Management (PERM) Council.
PERM Council Mission Statement
The goal of PERM is to provide overarching leadership and coordination of government and industry Pb-free electronics risk management activities to leverage the commercial supply chain for the aerospace, defense and high performance electronics communities.
PERM Council responsibilities include:
- Facilitate long-term aerospace, defense and high-performance electronics strategies and tactics to effectively deal with Pb-free electronics issues
- Develop and coordinate risk management approaches for the transition to Pb-free electronics that maintains:
- safety
- performance
- reliability
- affordability
Consider Joining the PERM Council Today
PERM Council Group
PERM is organized to provide industry leadership. The PERM Council, like all of the IPC Committees, uses IPC WORKS, a document management system which allows Council members to create, revise, and distribute documents in real-time fashion among these task teams:
Upcoming PERM Council Meeting Dates
The Council discusses lead-free conversion issues related to the safety, performance, reliability and affordability of electronics in the aerospace, defense, medical and other high-performance markets at several technical meetings throughout the year. Upcoming PERM meeting dates include the following:
Industry Related Documentation
Members of the PERM Council have had an active role in related Pb-free documentation published by other organizations, including the following:
NOTE: The links below will take you off the IPC.org website
Aerospace Industries Association – Joint Government and Industry Executive Form for Lead (Pb)-free Electronics Recommendations
Defense Acquisition University
- The Lead-Free Electronics Manhattan Project Phase 1 Report
- The Lead-Free Electronics Manhattan Project Phase 2 Report
Foresite, Inc. – What is Electrochemical Migration – Dendrite Shorting of Electronic Circuits?
Tin Whisker Risk Model Spreadsheet
Developed by BAE Systems under funding from the DoD Strategic Environmental Research Program (SERDP), a Tin Whisker Risk Model Spreadsheet has been developed that can be used to calculated the expected number of tin whisker shorts on one or more leaded components, based on user-specified part and lead geometry, whisker density, tin whisker length distribution, applied voltage, and conformal coating coverage. This tool is being provided by the University of Maryland’s Center for Advanced Life Cycle Engineering (CALCE) and can be accessed at https://web.calce.umd.edu/tin-whiskers/spreadsheet/
PERM Documentation and Specifications
The output of PERM participants has led to the generation of effective working documents, issues papers and direct communication with U.S. Department of Defense (DoD) officials as well as industry leaders.
The following documents can be found in the IPC Store:
IPC/PERM-2901, Pb-free Design and Assembly Implementation Guide
IPC-WP-012, Pb-free Electronics Risk Management (PERM) Council Pb-free Research Priorities
IPC/PERM-WP-022, Mitigation of Pure Tin Risk by Tin-Lead SMT Reflow - Results of an Industry Round-Robin - Final Report
The following documents can be found at another location which will take you off the IPC.org website. Please use this link PERM documents for purchase of these documents:
GEIA-STD-0005-1 Performance Standard for Aerospace and High Performance Electronic Systems Containing Lead-Free Solder
GEIA-STD-0005-2 Standard for Mitigating the Effects of Tin in Aerospace and High Performance Electronic Systems
GEIA-STD-0005-3 Performance Testing or Aerospace and High Performance Electronics Containing Lead-Free Solders and Finishes
GEIA-HB-0005-1 Program Management/Systems Engineering Guidelines for Managing the Transition to Lead-Free Electronics
GEIA-HB-0005-2 Technical Guidelines for Aerospace and High Performance Electronic Systems Containing Lead-Free Solder
GEIA-HB-005-3 Rework and Repair Handbook to Address the Implications of Lead-Free Electronics and Mixed Assemblies in Aerospace and High Performance Electronic Systems
GEIA-STD-0006 Requirements for Using Robotic Hot Solder Dip to Replace the Finish on Electronic Piece Parts
Upcoming PERM Council Meeting Dates
The Council discusses lead-free conversion issues related to the safety, performance, reliability and affordability of electronics in the aerospace, defense, medical and other high-performance markets at several technical meetings throughout the year. Upcoming PERM meeting dates include the following:
Tin Whisker Risk Model Spreadsheet
Developed by BAE Systems under funding from the DoD Strategic Environmental Research Program (SERDP), a Tin Whisker Risk Model Spreadsheet has been developed that can be used to calculated the expected number of tin whisker shorts on one or more leaded components, based on user-specified part and lead geometry, whisker density, tin whisker length distribution, applied voltage, and conformal coating coverage. This tool is being provided by the University of Maryland’s Center for Advanced Life Cycle Engineering (CALCE) and can be accessed at https://web.calce.umd.edu/tin-whiskers/spreadsheet/
PERM Documentation and Specifications
The output of PERM participants has led to the generation of effective working documents, issues papers and direct communication with U.S. Department of Defense (DoD) officials as well as industry leaders.
The following documents can be found in the IPC Store:
IPC/PERM-2901, Pb-free Design and Assembly Implementation Guide
IPC-WP-012, Pb-free Electronics Risk Management (PERM) Council Pb-free Research Priorities
IPC/PERM-WP-022, Mitigation of Pure Tin Risk by Tin-Lead SMT Reflow - Results of an Industry Round-Robin - Final Report
The following documents can be found at another location which will take you off the IPC.org website. Please use this link PERM documents for purchase of these documents:
GEIA-STD-0005-1 Performance Standard for Aerospace and High Performance Electronic Systems Containing Lead-Free Solder
GEIA-STD-0005-2 Standard for Mitigating the Effects of Tin in Aerospace and High Performance Electronic Systems
GEIA-STD-0005-3 Performance Testing or Aerospace and High Performance Electronics Containing Lead-Free Solders and Finishes
GEIA-HB-0005-1 Program Management/Systems Engineering Guidelines for Managing the Transition to Lead-Free Electronics
GEIA-HB-0005-2 Technical Guidelines for Aerospace and High Performance Electronic Systems Containing Lead-Free Solder
GEIA-HB-005-3 Rework and Repair Handbook to Address the Implications of Lead-Free Electronics and Mixed Assemblies in Aerospace and High Performance Electronic Systems
GEIA-STD-0006 Requirements for Using Robotic Hot Solder Dip to Replace the Finish on Electronic Piece Parts